Project Planning
Hygiene
In order to maintain a clean and hygienic environment, it is essential that drainage elements are designed and manufactured to minimise bacteria traps.
ACO Gully is designed for optimum hygiene performance, taking into account guidelines described in EN 1672, EN ISO 14159 and the European Hygienic Engineering and Design Group (EHEDG).
EN 1672 and EN ISO 14159 are standards that set out hygiene requirements for use in food processing.
EHEDG is a consortium of food industries, public health authorities, research institutes and equipment manufacturers. Their mission is to promote hygiene through improved hygienic engineering and design relating to all aspects of food manufacture. EHEDG principles are being recognised by designers and planners worldwide, including Australia.
Slip resistance
Slip resistant grates are recommended for installation in commercial kitchen and food processing area’s to reduce the risk of serious injury were high temperature food and equipment is used.
Slip resistance is becoming a bigger concern for the Australian design community as litigation around the topic rises and pressure is being placed on the specifier to correctly specify all floor materials according to the Standards.
There can be a tendency to over specify the grates slip resistance when compared to the surrounding flooring, as it is perceived as the slippery part of the design.
However, the grate and adjacent floor material should have the same level of slip resistance as rapid changes in surface roughness can create slips and trips. AS 4586 is the slip resistant standard and outlines the test methodologies for different applications.
There are three tests that are most relevant to grates: oil wet ramp, wet barefoot and wet pendulum.
The oil wet ramp test is designed for industrial and commercial environments where there is likely to be oil on the floor. This is an inclining platform test, where a test person is harnessed and walks back and forth across the test material on a ramp in a specific safety shoe. The ramp is gradually inclined until the test person feels they will fall. The test is repeated three times and a median value is awarded. This has ratings of R9 to R13, with R13 as the highest rating.
The wet barefoot test is designed for wet areas with bare feet, like pools or changing rooms and it is therefore not a suitable test for commercial kitchens as it does not reflect the application. Like the oil wet ramp test, it is also an inclining platform test, but uses bare feet, with water and no oil to simulate these environments. This test has three categories of slip resistance, A, B and C, with C being the highest rating.
The wet pendulum test is most suited to areas that get wet in rain and trafficked by worn heels, like pedestrian areas and building entries. The rating system is P0-P5, with P5 being the highest rating. Although this does not represent a commercial or industrial food environment, it is widely used in litigation cases as the test device is portable and slip resistance can be tested in-situ.
Stainless steel and nitrile rubber are easy to clean. Washing with soap or a mild detergent and warm water, followed by a clean water rinse is usually adequate for most industrial applications. An enhanced aesthetic appearance will be achieved if the cleaned surface is finally wiped dry.
Acids should only be used for on-site cleaning when all other methods have been proved unsatisfactory. Rubber gloves should be used and care taken to ensure acid cleaners are not spilt over adjacent areas.
Special precautions are necessary with oxalic acid and solvents should not be used in closed spaces without adequate ventilation. Manufacturer’s directions should always be followed.
If the suggestions in the table below have been attempted and the result is still unsatisfactory, stainless steel is able to be mechanically cleaned by specialists on site. Please contact ACO for further information.
Problem | Cleaning agent | Comment |
---|---|---|
Routine cleaning, all finishes. | Soap or mild detergent and water (such as dishwashing liquid). | Sponge, rinse with clean water, wipe dry if necessary. |
Fingerprints, all finishes. | Soap or warm water or organic solvent (e.g. acetone, alcohol). | Rinse with clean water, wipe dry if necessary. |
Stubborn stains and discolouration. | Mild cleaning solutions or cream cleanser. | Rinse well with clean water and wipe dry. |
Oil and grease marks, all finishes. | Organic solvents (e.g. acetone, alcohol). | Clean after soap and water, rinse with cleanwater and dry. |
Rust and other corrosion products. | Oxalic acid. | Rinse well with clean water. The cleaning solution should be applied with a swab and allowed to stand for 15–20 minutes before being washed away with water. Use a mild cleaning solution to give a final clean if required. |
Scratches on brush (satin) finish. | Household synthetic fibre scouring pads. | Do not use ordinary steel wool, as particles can become embedded in stainless steel and cause surface problems. For deeper scratches; apply scourer in direction of polising. Clean with soap or detergent as per routine cleaning. |
Inspection and rodding
A rodding eye is an access point in a drainage system that is used to inspect and rod blocked drainage pipes. This is useful when pipes are located in areas where usual inspection and rodding are not possible, for example with a fixed (secondary) strainer.
Pipe DN/OD (mm) | Weight (kg) | Stainless steel grade | Part No. |
---|---|---|---|
100/110 | 1.5 | 316 | 416998 |
ACO Gully 157 – fixed height
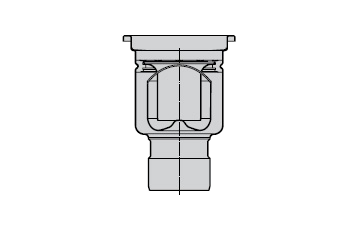
Flow rate [L/s] | ¹With Internal FAT | ²Without Internal FAT |
|
DN 100 | Vertical | 3.5 | 12.0 |
ACO Gully 157 – adjustable height
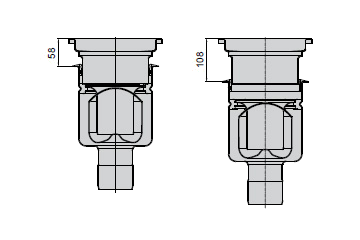
Flow rate [L/s] | ¹With Internal FAT (min) | ¹With Internal FAT (max) | ²Without Internal FAT | |
DN 100 | Horiz. | 2.8 | 3.3 | 10.2 |
Vert. | 3.5 | 4.0 | 12.6 |
ACO Gully 218 – fixed height
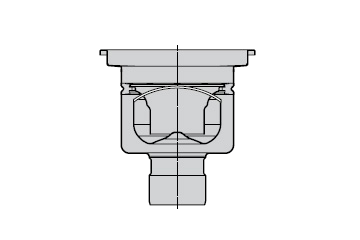
Flow rate [L/s] | ¹With Internal FAT | ²Without Internal FAT |
|
DN 100 | Vertical | 4.6 | 12.1 |
DN 150 | Vertical | 4.6 | 25.8 |
ACO Gully 218 – adjustable height
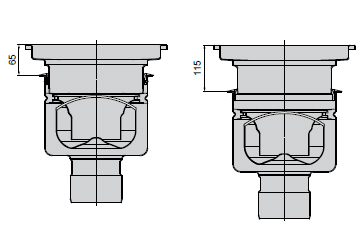
Flow rate [L/s] | ¹With Internal FAT (min) | ¹With Internal FAT (max) | ²Without Internal FAT | |
DN 100 | Vertical | 5.0 | 5.5 | 27.1 |
The corrosion resistance information contained within this table is indicative only.
All data is based on reactions noted at an ambient temperature of 20°C. Higher temperatures will generally reduce the corrosion resistance of the materials.
Typical factors that affect material selection:
- type(s) of chemical(s) and % composition in the liquid
- concentration percentages
- contact time with trough system
- temperatures of liquid flowing into the trough
- flushing system employed o clear liquids from the system
- type of cleaning agent (see Care & Maintenance)
- grate, locking mechnism and trash basket materials
- sealant for compatibility, if applicable
Test samples should be used for final determination of chemical resistance, contact ACO.
![]() | Recommended |
![]() | Suitable, contact ACO for further advice |
![]() | Not recommended |
![]() | No data available |
Reagent | Stainless Steel 304 | Stainless Steel 316 |
---|---|---|
Acetic Acid 20% | ![]() | ![]() |
Acetic Acid 80% | ![]() | ![]() |
Acetone | ![]() | ![]() |
Alcohol (Methyl or Ethyl) | ![]() | ![]() |
Aluminium Chloride | ![]() | ![]() |
Aluminium Sulphate | ![]() | ![]() |
Ammonia Gas (Dry) | ![]() | ![]() |
Ammonium Chloride | ![]() | ![]() |
Ammonium Hydroxide | ![]() | ![]() |
Ammonium Nitrate | ![]() | ![]() |
Ammonium Phosphate | ![]() | ![]() |
Ammonium Sulphate | ![]() | ![]() |
Ammonium Sulphide | ![]() | ![]() |
Amyl Chloride | ![]() | ![]() |
Aniline | ![]() | ![]() |
Barium Chloride | ![]() | ![]() |
Barium Hydroxide 10% | ![]() | ![]() |
Barium Sulphate | ![]() | ![]() |
Barium Sulphide | ![]() | ![]() |
Beer | ![]() | ![]() |
Beet Sugar Liquors | ![]() | ![]() |
Benzene | ![]() | ![]() |
Benzoic Acid | ![]() | ![]() |
Bleach -12.5%Active C1 | ![]() | ![]() |
Boric Acid | ![]() | ![]() |
Bromic Acid | ![]() | ![]() |
Bromine Water | ![]() | ![]() |
Butane | ![]() | ![]() |
Calcium Carbonate | ![]() | ![]() |
Calcium Chloride | ![]() | ![]() |
Calcium Hydroxide | ![]() | ![]() |
Calcium Hypochlorite | ![]() | ![]() |
Calcium Sulphate | ![]() | ![]() |
Cane Sugar Liquors | ![]() | ![]() |
Carbon Acid | ![]() | ![]() |
Carbon Bisulphide | ![]() | ![]() |
Carbon Dioxide | ![]() | ![]() |
Carbon Monoxide | ![]() | ![]() |
Carbon Tetrachloride | ![]() | ![]() |
Caustic Potash | ![]() | ![]() |
Caustic Soda | ![]() | ![]() |
Chloride (Dry) | ![]() | ![]() |
Chloride (Wet) | ![]() | ![]() |
Chloroacetic Acid | ![]() | ![]() |
Chlorobenzene | ![]() | ![]() |
Chloroform | ![]() | ![]() |
Chrome Acid 50% | ![]() | ![]() |
Chromic Acid 10% | ![]() | ![]() |
Citric Acid | ![]() | ![]() |
Copper Chloride | ![]() | ![]() |
Copper Cyanide | ![]() | ![]() |
Copper Nitrate | ![]() | ![]() |
Copper Sulphate | ![]() | ![]() |
Cottonseed Oil | ![]() | ![]() |
Cresol | ![]() | ![]() |
Cyclohexanone | ![]() | ![]() |
Cyclorexanol | ![]() | ![]() |
Dimethyleanine | ![]() | ![]() |
Dionylphalate | ![]() | ![]() |
Disodium Phosphate | ![]() | ![]() |
Distilled Water | ![]() | ![]() |
Ethyl Acetate | ![]() | ![]() |
Ethylene Chloride | ![]() | ![]() |
Ethylene Glycol | ![]() | ![]() |
Ethylene Glycol | ![]() | ![]() |
Ferric Sulphate | ![]() | ![]() |
Fluorene Gas (Wet) | ![]() | ![]() |
Formaldehyde (37%) | ![]() | ![]() |
Formic Acid (90%) | ![]() | ![]() |
Freon 12 | ![]() | ![]() |
Fruit Juices and Pulp | ![]() | ![]() |
Furfural | ![]() | ![]() |
Gasoline (Refined) | ![]() | ![]() |
Glucose | ![]() | ![]() |
Glycerine | ![]() | ![]() |
Hydrobromic Acid (20%) | ![]() | ![]() |
Hydrochloric Acid (40%) | ![]() | ![]() |
Hydrocyanic Acid | ![]() | ![]() |
Hydrogen Peroxide (90%) | ![]() | ![]() |
Hydroquinone | ![]() | ![]() |
Hypochlorous Acid | ![]() | ![]() |
Iodine | ![]() | ![]() |
Kerosene | ![]() | ![]() |
Lactic Acid 25% | ![]() | ![]() |
Linseed Oil | ![]() | ![]() |
Liqueurs | ![]() | ![]() |
Magnesium Chloride | ![]() | ![]() |
Magnesium Sulphate | ![]() | ![]() |
Maleic Acid | ![]() | ![]() |
Methyl Chloride | ![]() | ![]() |
Methyl Ethyl Ketone | ![]() | ![]() |
Milk | ![]() | ![]() |
Minerals Oils | ![]() | ![]() |
Muriatic Acid | ![]() | ![]() |
Nickel Chloride | ![]() | ![]() |
Nickel Sulphate | ![]() | ![]() |
Oils and Fats | ![]() | ![]() |
Oleic Acid | ![]() | ![]() |
Oleum | ![]() | ![]() |
Oxalic Acid | ![]() | ![]() |
Palmitic Acid 10% | ![]() | ![]() |
Perchloric Acid 10% | ![]() | ![]() |
Perchloric Acid 70% | ![]() | ![]() |
Petroleum Oils (Sour) | ![]() | ![]() |
Phenol 5% | ![]() | ![]() |
Phosphorous Trichloride | ![]() | ![]() |
Photographic Solutions | ![]() | ![]() |
Picric Acid | ![]() | ![]() |
Plating Solutions | ![]() | ![]() |
Potassium Carbonate | ![]() | ![]() |
Potassium Chloride | ![]() | ![]() |
Potassium Cyanide | ![]() | ![]() |
Potassium Dichromate | ![]() | ![]() |
Potassium Hydroxide | ![]() | ![]() |
Potassium Permanganate | ![]() | ![]() |
Potassium Sulphate | ![]() | ![]() |
Propane Gas | ![]() | ![]() |
Propyl Alcohol | ![]() | ![]() |
Sea Water | ![]() | ![]() |
Sewage | ![]() | ![]() |
Silver Nitrate | ![]() | ![]() |
Silver Sulphate | ![]() | ![]() |
Sodium Bicarbonate | ![]() | ![]() |
Sodium Bisulphite | ![]() | ![]() |
Sodium Carbonate | ![]() | ![]() |
Sodium Cyanide | ![]() | ![]() |
Sodium Ferrocyanide | ![]() | ![]() |
Sodium Hydroxide | ![]() | ![]() |
Sodium Hypochlorite | ![]() | ![]() |
Sodium Sulphate | ![]() | ![]() |
Sodium Sulphide | ![]() | ![]() |
Sodium Sulphite | ![]() | ![]() |
Sodium Thiosulphate | ![]() | ![]() |
Stannous Chloride | ![]() | ![]() |
Stearic Acid | ![]() | ![]() |
Sulphite Liquor | ![]() | ![]() |
Sulphurous Acid | ![]() | ![]() |
Sulphur | ![]() | ![]() |
Sulphur Dioxide (Dry) | ![]() | ![]() |
Sulphur Dioxide (Wet) | ![]() | ![]() |
Sulphuric Acid 50% | ![]() | ![]() |
Sulphuric Acid 70% | ![]() | ![]() |
Sulphuric Acid 93% | ![]() | ![]() |
Tannic Acid | ![]() | ![]() |
Tanning Liquors | ![]() | ![]() |
Tartaric Acid | ![]() | ![]() |
Toluene | ![]() | ![]() |
Trichloroethylene | ![]() | ![]() |
Triethanolamine | ![]() | ![]() |
Trisodium Phosphate | ![]() | ![]() |
Turpentine | ![]() | ![]() |
Urea | ![]() | ![]() |
Urine | ![]() | ![]() |
Vinegar | ![]() | ![]() |
Water (Fresh) | ![]() | ![]() |
Water (Mine) | ![]() | ![]() |
Water (Salt) | ![]() | ![]() |
Whisky | ![]() | ![]() |
Wines | ![]() | ![]() |
Xylene | ![]() | ![]() |
Zinc Chloride | ![]() | ![]() |
Zinc Sulphate | ![]() | ![]() |
There is no Australian Standard that governs the performance of floor gullies. ACO believes that EN 1253, specifically written to regulate these types of products, is the most appropriate International Standard.
EN 1253 – Gullies for buildings 1. Scope
‘This Standard classifies gullies, gives guidance for places of installation and specifies requirements for construction,design, performance and marking of factory gullies, irrespective of material,for use in drainage systems operating under gravity including siphonic systems.’
The table below is created to give designers,installers and users assistance in selecting the correct product.The table is based on loadings outlined in EN 1253 and is cross referenced with AS 3996 – Access Covers and Grates,the most relevant Australian Standard for load classifications. ACO has gained NATA accreditation (No.15193) for its testing laboratory and can provide test reports to EN 1253.
Standards only give an objective means for comparing products. There are a number of key factors affecting a product’s resistance to load and additional consideration must be given to:
- Type of traffic: Consider the weight of loads being carried, for example forklifts, trolleys and trucks.
- Wheel type: Solid tyres exert more stress through smaller contact areas than pneumatic tyres, so a heavier duty grate may be required. Note, laden trolleys can intensify the load.
- Frequency and speed of traffic: More frequent and faster traffic can intensify the load.
- Position of gully: If the product is positioned where traffic will be turning or braking, or if it is installed at the bottom of a ramp, the gully will be subjected to extreme forces.
1 Draft prEN 1253
Note: For higher load classes contact ACO.